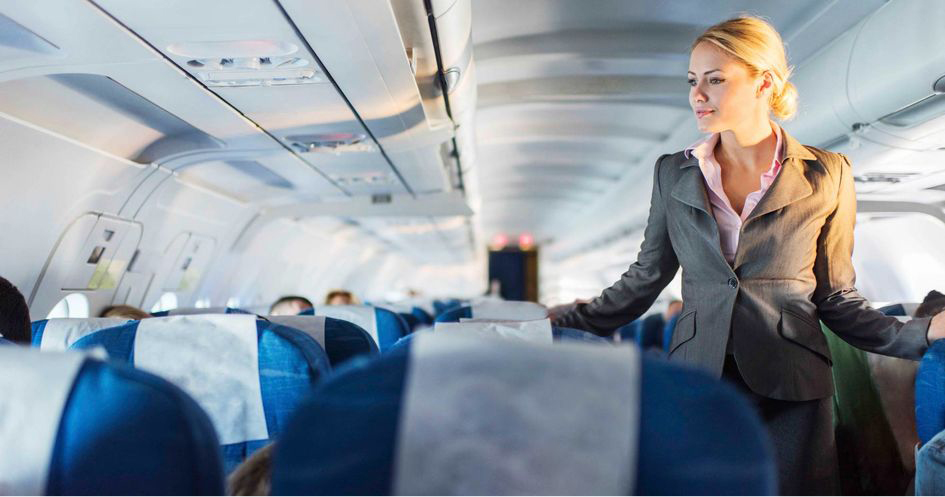
航空機部品メーカーB社 設計部
炎(Flame)が出ない、煙(Smoke)が出ない、
毒性ガス(Toxicity)を発生しない!
安全基準を満たした、まったく新しい航空機内装向けコンポジット部品用コア材とは
解決
解決のポイント
ロハフォーム(ROHAFOAM®)は厳しいFST規格に合格、デザイン自由度が高い
二次加工が不要で低コスト、接着フィルムやパテ埋めが不要で軽量化が期待できた
コア材の成形から試験用のデータ提出までワンストップで提供可能
ハニカムコアの課題を解決した、まったく新しい発泡コア材「ロハフォーム」
あるとき、M氏は以前から知っていた圧力隔壁などに使用される発泡コア材「ロハセル®」に注目します。ロハセル®は航空機、ロケット、レーシングカー、CT機のベッド、スピーカー振動板など、多種多様な用途に優れたコンポジットコア材として使用されていました。しかし、アクリル系の発泡体であるため、FST規格を満たすことができず、機内の部品には使用することができませんでした。
当ては外れたものの、発泡コア材の可能性を感じたM氏は情報収集を続けました。そして、ドイツのエボニック社のウェブサイトでロハセル®とは別に「ロハフォーム(ROHAFORM®)」という新しい素材を見つけます。
「ロハフォームはまったく新しい発泡コア材で、厳しいFST規格に合格しており、設計自由度が高いことが記載されていました。そこで、日本の販売元であるポリプラ・エボニックに問い合わせてみることにしました」(M氏)
営業担当者によれば、ロハフォームは機内シート、オーバーヘッドビン、ラバトリーの壁、ギャレー、搭乗口周り、パイロットシート、窓枠のパネルなど、航空機内での多様な用途に適しており、現在さまざまなメーカーで製品開発が進んでいるそうです。
「デザイン自由度が高く、成形時にインサート部品をセッティングできるため二次加工が不要となり、コストを抑えることが可能だとわかりました。またハニカムコアで使用される表皮材の接着のためのフィルムや、強度が必要な部分や端部のパテ埋めが必要なく、軽量化も期待できます。さらに、素材のみの提供ではなく、コア材の成形から試験用のデータ提出までワンストップでお願いできることは非常に魅力的でしたね」(M氏)
M氏はロハフォームの採用について、上長に掛け合います。そして、FST基準を満たしていること、難燃性および軽量化への期待、他コア材を使用した最終製品で比較して製造コストが抑えられることなどが認められ、製品開発を進めることが決定しました。
現在、予定通り順調に試作が進められています。