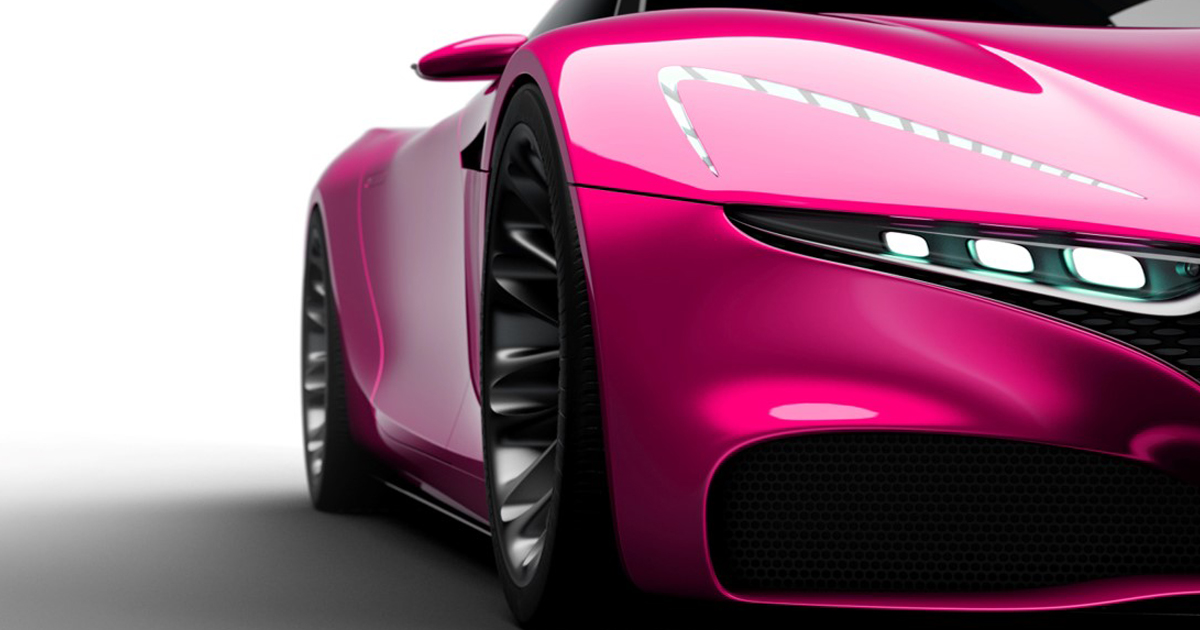
車載用部品メーカーL社 設計開発部
モーターやバッテリー冷却装置用の配管を軽量化したいが、課題が山積して…
樹脂メーカーと共同開発?従来の金属、ゴム使用に比べ最大で約50%の軽量化に期待が!
解決
解決のポイント
耐熱性や低温衝撃性、耐薬品性など材料物性的な性能の担保も必須条件
テクニカルセンターを活用した共同開発で、時間、品質など大幅な効率化を実現
従来の金属、ゴム使用に比べ最大で約50%の軽量化が期待できることが判明
テクニカルセンターを活用した共同開発で、時間、品質ともに大幅な効率化を実現!
「自社のポリアミド樹脂を使った冷却配管なら、大幅な軽量化が可能です」相談を受けたポリプラ・エボニックの担当者から早々に、可能性のある回答をもらえました。同時に、この樹脂がもつパフォーマンスレベルの説明も受けることができました。
「樹脂の存在やパフォーマンスの説明に魅力を感じましたが、なにより、欧州車の樹脂配管としてすでに実績があるという事例は大きかったですね」(S氏)
さらに担当者から、想定される流体温度に最適な2つの樹脂グレードを使って、今回の配管の共同開発を提案されました。中低温度域では単層チューブを、高温度域では多層チューブを使い分けることや、兵庫県の網干にあるポリプラ・エボニックのテクニカルセンターを拠点に活用するという内容でした。
今回の場合、提案通りに進めたほうが開発期間や品質などの面で、大幅な効率化が図れると考えたS氏。上長の許可を取り付け、すぐに共同開発をスタートさせます。この判断は、のちに大成功につながりました。国内で試作 評価 再試作が繰り返せるため、スピーディな開発を実現でき、品質向上に寄与しました。また、センターには5層の押出機が設置されており、多層チューブの循環試験や、層間接着強度測定なども繰り返し実施ができ、開発は順調に進んでいきました。
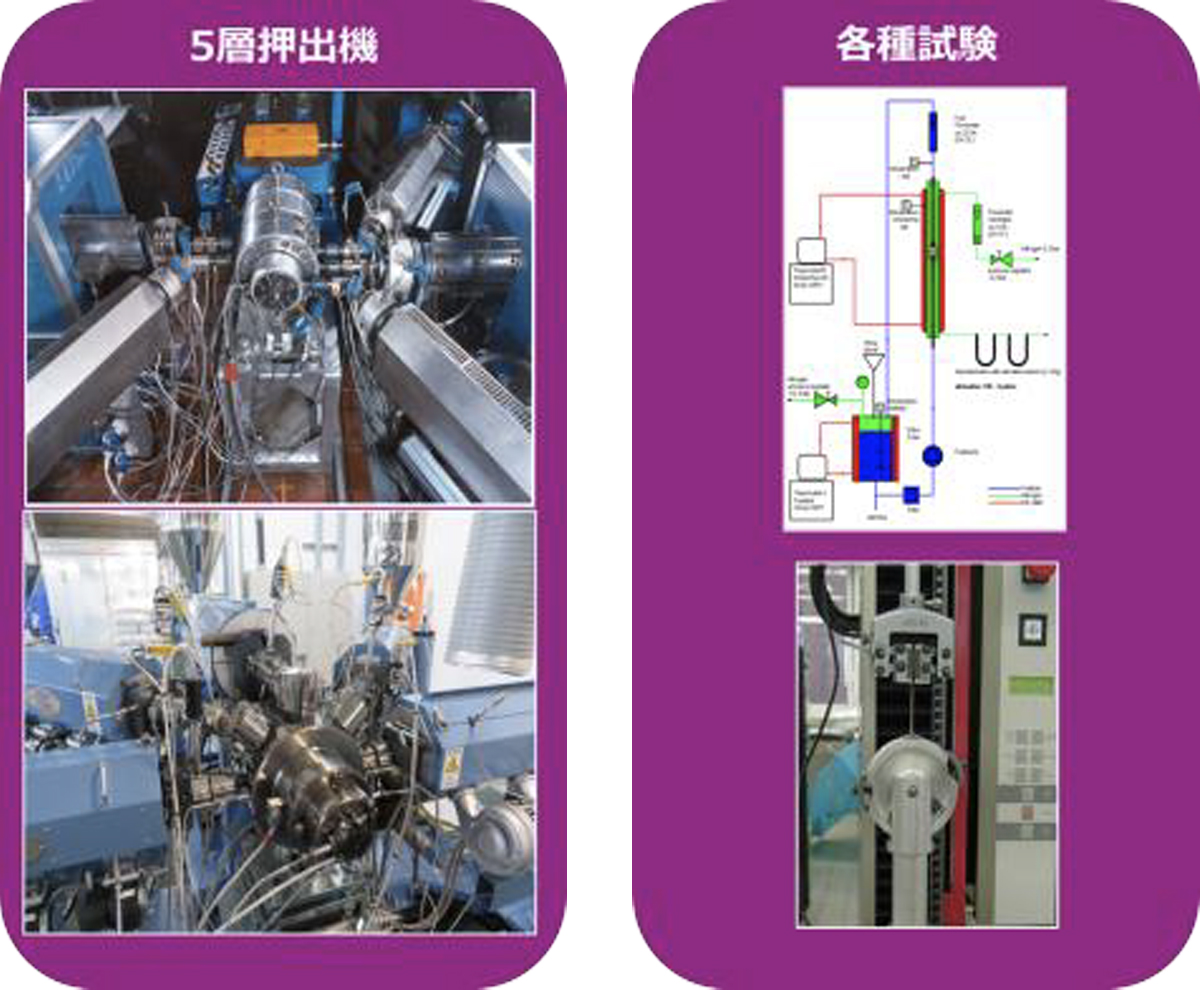
ベースは、ポリプラ・エボニックベスタミド®の豊富なグレードから、今回の仕様に最適なものを選定。すると、できあがった配管は従来の金属、ゴム使用に比べ最大で約50%の軽量化が期待できることがわかりました。また、課題だった物性的なスペックの担保や機能面も一気に解決できたのでした。早速、試作した配管を取引先にテストしてもらったところ、重さ、物性とも評価は上々の結果を得ることができました。
現在は、量産に向けて最終の調整をポリプラ・エボニックと共同で進めています。