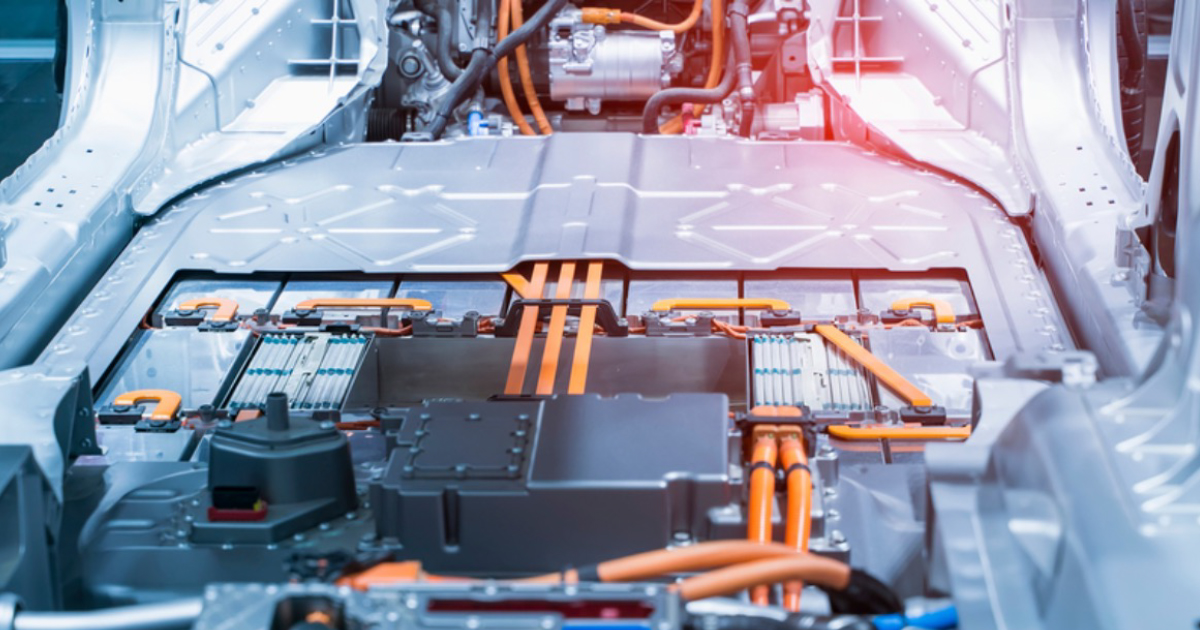
ワイヤーハーネス製造 H社 設計開発部
高性能なEV向けに、ハーネスのさらなる高出力化とそれに伴う省スペース化が必要…
解決策は、高い難燃性を持ったポリアミド12を用いた押出被覆のバスバーの活用だった!
背景
人気EVの次モデルが、航続距離アップなどのために電池容量を大型化することから、現モデルのワイヤーハーネスより高出力対応をしてほしいとの依頼が、OEMメーカーからH社に入った。しかし、既存のハーネス技術では、ハーネスの径が大幅に太くなり運転席などのキャビンスペースを圧迫してしまうため、代わりにバスバーの使用を考えた。一方で、近年の中国EV市場は拡大傾向にあり、今後バスバーのニーズはますます高まるとともに複雑な形状を要求される。ところが、そこに難題が待ち構えていた。
課題
バスバーへの代替案は良かったが、被膜する樹脂の問題が山積みでこのままでは…
バスバーの使用を想定した場合、1m以上の長尺かつ、配線レイアウトの都合上バスバーに複雑な曲げ形状などを施す必要がありました。また、バスバー自体への絶縁保護と、人が触れてはいけないことを示す警告色として、オレンジ色でバスバーへ何らかの樹脂を被覆する必要があったのです。
この難題について、設計担当者T氏は、当時の様子を以下のように振り返ります。
「過去にもバスバーの被覆については、短い部品の場合、粉体塗装やインサート成形などで対応したことがありました。しかし、今回は1m以上の長尺な部品に樹脂での被覆が必要になります。現行の生産方法では、部品サイズが大き過ぎるため、生産設備上、弊社でも協力会社でも対応は難しそうです。また、複雑な曲げ形状のバスバーに、均一に樹脂での被覆をすることは、かなり難しいことが想定されました」
これら生産工程の課題以外にも、バスバーの被覆には耐熱性、絶縁性、難燃性、耐薬品性など多くの条件が求められていました。
困り果てたT氏がインターネットで解決の糸口を検索したところ、ポリプラ・エボニックが先日の展示会で押出被覆のバスバーを紹介している記事を発見しました。
課題のポイント
生産プロセス上、既存の粉体塗装、インサート成形では長尺なバスバー部品の被覆が難しい
さらに、複雑な曲げ形状を施したバスバーの場合、均一な厚みでの被覆が難しい
その他にも耐熱性、絶縁性、難燃性、耐薬品性などの要求性能を満たす樹脂が必要